**Best Practices for POD Sellers to Ensure Quality T-Shirt Production**
**One of the best ways for any entrepreneur in the competitive e-commerce world to build a loyal customer base is by offering them the highest-quality products or services. Especially for POD sellers focused on T-shirts, delivering a high-quality product is crucial for customer satisfaction and brand reputation. To help POD startups meet the requirements, in this article, [Lion King Shirt](https://forum.studio-397.com/index.php?threads/why-lion-king-shirt-are-the-perfect-blend-of-fun-and-fashion.64996/) will explore the essential strategies for maintaining top-notch quality in T-shirt production.**
**Partnering with Reliable POD Suppliers and Manufacturers**
This is the first and also the fundamental step for your products when it comes to quality. Since the quality of your T-shirts depends on the manufacturers, you should spend a little more time researching potential partners and reading reviews from past customers thoroughly.
Once you’ve chosen your suppliers and manufacturers, you need to check if their capacity matches your production demands and have stringent quality control processes. After that, you should understand the printing methods that the provider specializes in, such as direct-to-garment or screen printing. For example, for one that uses direct-to-garment, their digital printing will apply ink directly onto the fabric, providing vibrant colors and soft prints, while screen printing lays down a thicker layer of ink, ideal for bold graphics and large coverage designs. Understanding these basics will help you make informed decisions about printing methods that best suit your designs and quality standards. With quality focused providers, there will be a great investment in the latest printing equipment and techniques.
Also, considering the quality and variety of blank T-shirts offered is recommend. You should seek providers that use name-brand, high-thread-count fabrics tested for durability and softness. The fabric choice will significantly impact the garment's comfort, durability, and overall appearance.
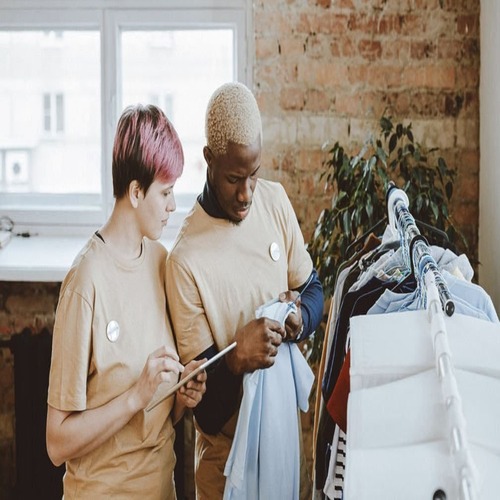
_A Manufacturers with extensive capabilities ensures flexibility and quality_
**Selecting High-Quality Materials and Artwork**
After selecting the ideal supplier, clear communication about your expectations for T-shirts with specific details like material blend, weight, cut, and size dimensions by providing comprehensive production specifications is necessary. A POD seller should provide printing specifics, including the number of colors, ink types, print locations, distressing effects, and white ink usage for dark shirts. They should also provide guidance on packaging like polybags or boxes, tissue paper, hang tags, and branding stickers. As the more information supplied upfront, the less likely there will be surprises or variations from order to order. If available, request a spec sheet template from the provider to ensure all pertinent details are covered.
Moreover, even the best POD supplier cannot deliver quality results without high quality artwork. Therefore, images should be in sharp focus and text must be vector-based. It’s important to submit artwork files in the format and minimum resolution required by the provider, typically 300 dpi for images and vector files for text. While JPEG is suitable for photographs, EPS and PNG are better for graphics with flat colors. Sellers need to double-check that CMYK colors are used, not RGB. Making the artwork print-ready avoids quality issues like pixelation that compromise the end product. To truly **[Wear your passions with POD T-shirt designs from LionKingShirt](https://substack.com/home/post/p-155325367)**, attention to detail in material selection and artwork quality is crucial for achieving exceptional results.
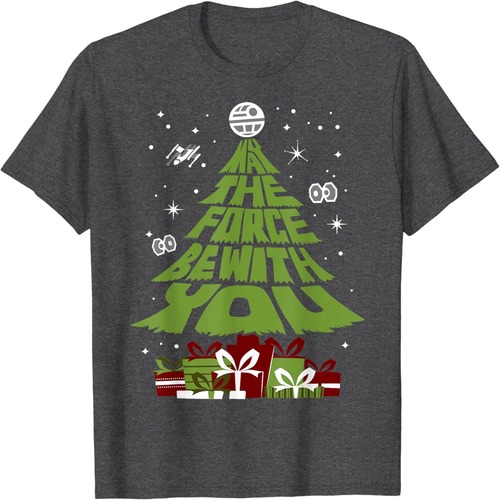
_Ensure high resolution and appropriate file formats for optimal print quality_
**Quality Control Measures**
**1\. Requesting Samples and Test Prints**
Before fully launching the final result of your T-shirt batch, having the manufacturer produce samples using your exact specifications and artwork is a must. Physically inspecting a few printed shirts allows verification of print alignment, image sharpness, text legibility and color accuracy. You may request adjustments at this stage if any element needs tweaking. Testing different blank shirt colors and printing on both front and back designs can highlight potential quality issues. Your batch can only move to full production after approving the test print results. The time and cost invested will pay pidends in heading off mistakes before they multiply.
**2\. Inspecting Quality During Production**
Even after approving samples, a smart POD T-shirt provider should stay vigilant in monitoring lead times and production quality. Plus, you can make an agreement with the provider for routine inspections that include sharing photos of random T-shirts pulled during printing to check whether graphic alignment, proportions and imprint colors match perfectly across samples. Also, do not forget to verify consistent sizing and fabric quality. For large orders, consider having a third-party quality control firm randomly select and assess shirts after printing. Following up quickly on any defects identified enables you to prevent larger problems down the line.
**3\. Learning and Improving Through Experience**
Communication channels are used not only to ensure expectations can be met, but also to adopt a mindset of continuous quality improvement with your POD partner. By exchanging feedback, POD providers can fix any repeating issues that slip past inspections and keep notes of adjustments made and lessons learned.
Over time, keep in mind that you should refine your artwork practices and production specifications to minimize defects. As your sales volume with a provider grows, negotiate improved quality control terms in your production agreements. With strategic planning, you can leverage your purchasing power to gain greater oversight on the production floor and ensure compliance with industry standards. Investing time upfront establishing quality assurance practices reduces obstacles for everyone in the long run.
To sum up, producing quality printed T-shirts through on-demand fulfillment requires careful provider selection, detailed specifications, rigorous inspections, and a passion for excellence. By proactively managing the production process, POD sellers like **[Lion King Tee Shirts](https://eggs.mu/artist/lionkingshirt/)** can delight customers and protect their brand reputation by consistently delivering high-quality products.